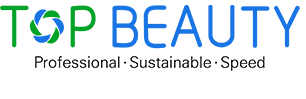
2013-12-26 09:58:20
Coty Saves Over $270,000 with Statistical Process Control
2013-12-26 09:58:20
By Steve Wise, vice president of statistical methods, InfinityQS International, Inc.A leader in the global beauty and fragrance industry, Coty exhibits innovation and a drive to capture trends sooner, thereby creating enduring brands that speak to the aspirations and lifestyles of today's consumers. ( looking for lipstick packaging manufacturer?)
Fueled by passion, creative freedom, and an entrepreneurial spirit, Coty has built a unique portfolio of beauty brands that have produced some of the strongest consumer franchises in history. The company’s products span three categories of fragrances, color cosmetics, and skin and body care, with adidas, Calvin Klein, OPI, philosophy, Chloé, Davidoff, Playboy, Rimmel, Marc Jacobs, and Sally Hansenrounding out its top 10 brands.
The Beauty of Continuous Improvement (looking for compact case manufacturer?)
Coty’s strong emphasis on continuous improvement led to the evaluation of its filling process, which determined that a higher level of waste was being generated than expected.
This was due in part to some lines overfilling containers to ensure aesthetic fills were met, ultimately leading to higher expenses on supplies - and presented a significant opportunity to reduce overfill and save money. However, the company did not have the necessary historical data on these lines for process engineers and quality professionals to truly understand the entire problem and develop a viable solution.
Innovation Is the Answer
The manufacturing team at Coty’s Sanford, N.C., facility turned to statistical process control (SPC) analysis to better understand scrap at the point of manufacture on these filling lines. With a proven Manufacturing Intelligence platform powered by a centralized SPC analysis engine, Coty could determine ways toreduce liquid scrap and better understand process capability. (looking for eye shadow case?)
An SPC Fill Height Project was incrementally implemented on 12 fragrance lines with target amounts set for every SKU (2,600 parts), control limits for each product and line combination (filling variation), and specification limits (min and max fill height levels).
The process also included training for more than 100 users, from line operators and quality inspectors to managers and directors. With a Manufacturing Intelligence platform, Coty found that it could consolidate all necessary key performance indicators (KPIs) into a single control chart for easy interpretation and analysis. (looking for mascara tubes?)
This intelligence allowed the company to eliminate the need for overproduction of liquid to compensate for overfilling, identified special cause variation vs. natural variation with real-time information of the process, and removed time-consuming, after-the-fact quality checks that did not add value.
“By incorporating a Manufacturing Intelligence platform with an SPC engine into our plant floor quality efforts, Coty has realized benefits across all parts of the value chain – from quality professionals that experience unprecedented database accuracy, to executives seeing financial savings,” said Romina Colautti, process engineer, Coty.
Manufacturing Intelligence Drives Cost Savings & ROI
Coty has seen significant financial and resource savings with the implementation of a real-time Manufacturing Intelligence platform. With an initial investment of $47,000, the carefully planned and executed projects have reduced variation, increased accuracy of set points, validated process capability, and reduced overfilling.
The SPC Fill Height project alone saved Coty over $270,000 by eliminating overfilling through more accurate fill heights. This resulted in a $220,000 return on investment in just two years.
LinkedIn